Bill of Materials SAP
Ask most business owners what they do for a living, and their response will be something about growing their business. Every production stage requires detailed records to ensure continuity, consistency, and improved business operation – from purchasing raw materials to manufacturing, assembling, and selling the finished products. Regardless, it’s often possible for small-to-medium-sized businesses to lose track of essential data at different phases within the multiple processes involved in production. So, we’ll highlight an important feature within SAP B1 – Bill of Materials.
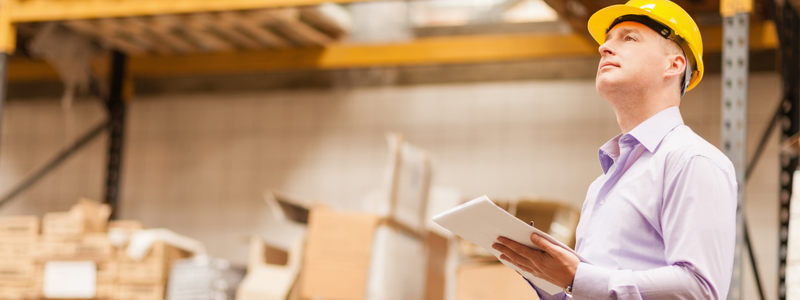
What is a Bill of Materials?
The SAP Business One is an enterprise resource planning (ERP) system with a feature to overcome the challenges of production – Bill of Materials (BOMs).
A Bill of Materials is a detailed list of components and quantities required to produce and assemble a finished good.
This SAP Business One element improves the overall production process and encourages efficiency, accuracy, and timeliness.
Overcome Business Challenges with Bill of Materials in SAP B1
Manufacturing businesses involve multiple aspects that require proper management and attention to detail.
It goes a long way to impact the growth and outcome of the company.
However, this segment of the business seems to have some of the biggest challenges in the industry.
Some include:
- Proper supervision of inventory across several warehouses
- Keeping and tracking inventory records
- Timely creation of raw materials and parts to fit the production schedule
- Access to real-time information
- Managing surplus or shortage inventory
Within these challenges most business owners face, employing sophisticated business management systems that support sharing the Bill of Materials presents a solution for manufacturers.
Some benefits of leveraging the shared BOM among employees such as the engineers and supply chain management includes:
- Free flow of business information
- Increased efficiency within business operations
- Higher productivity
- Gaining an edge in market competition through increasing prospects
How the BOM is Created in SAP
Once you create the Bill of Materials for the product, the header allows you to define the quantity of material you intend to produce.
Every other quantity is relative to the defined base quantity.
There may be multiple alternative Bill of Materials for a product that you can use based on the different production processes, validity areas, or lot sizes.
How the Bill of Materials SAP Works
While a company’s production process starts by procuring raw materials, the production order allows for documentation of every detail of production steps, the materials used, and the predefined time frame to create the product.
SAP Business One generates the Bill of Materials to show a complete reflection of the inventory of the production order, including all the raw materials and the cost required to build a product.
The bill of materials SAP arranges these items in a stratified hierarchy of the raw materials and sub-items needed for the finished product.
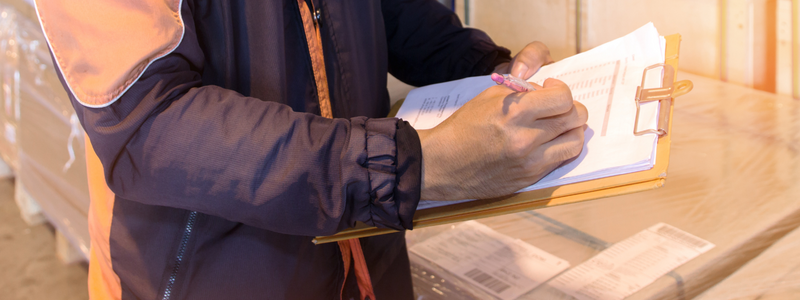
Types of Bills of Materials
Even though it’s possible to generate the Bill of Materials via manual entry, the production process is complex and vulnerable to errors. Therefore, implementing an integrated ERP system such as SAP Business One remains the most accurate and timely solution to these challenges.
Depending on the production process of your business, there are four main types of Bills of Material SAP applications, including:
Production Bill of Materials
SAP generates a production Bill of Materials for standard production orders, and Materials Requirements Planning (MRP) runs.
While the production BOM forms a list to make finished products the parent components, it lists the other items that complement the parent product as child components.
During production, you can transform these components into finished products.
Sales Bill of Materials
If the parent item is listed as a sales item instead of an inventory item, the SAP generates a Sales Bill of Materials. This means selecting the parent item in the sales document makes the child items appear as sub-items. At this stage in the sales document, you can edit the quantity of the sub-items, but you can no longer delete or add new child items to the package.
For instance, if a printer is a parent item, all necessary components within the printer go to the child item category.
Assembly Bill of Materials
Like the sales Bill of Materials, the assemble BOM shows a collection of items within a specific price set.
Here, you can manage the final product as a sales item and not an inventory item. The difference is that it shows only the finished product in the sales document, and the components don’t appear as sub-items as it does on sales BOM.
Template Bill of Materials
With no real restriction, the template BOM is more adaptable to allow the selection of any component as either parent or child item.
Template BOM shows the parent item on top and the child component below, and it’s useful for both production and sales documents. The flexibility of this type of BOM enables necessary modification within the documents by replacing, updating, or omitting the components.
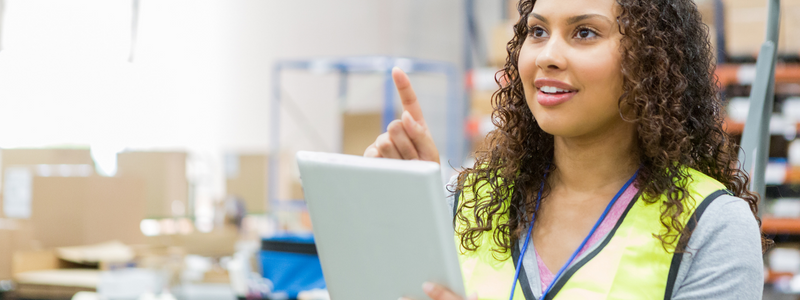
What Does This Mean for My Business?
Depending on your business, the Bill of Materials forms a structure for the complete list of items required to create and assemble your product. The makeup of this list includes the material number of each item, the quantity, and the unit of measure.
The Bill of Materials in SAP can be single-level and multi-level production where finished materials can contain semi-finished material which serves as components and raw material for the next level.
Here are some uses of the BOM in business:
- In production planning, BOM functions in purchase planning for raw materials and semi-finished products and component quantity for the demand of finished products.
- While calculating the standard cost for finished products, information from BOM makes it easy to roll up costs of production, from procuring raw materials to semi-finished and finished products.
- Ranging from the required quantity of raw material, the activities, and overhead cost, BOM records the production cost for each final good.
- BOM at all levels helps to detect and calculate shortage quantity in material requirement planning.
- Making material BOM in the production planning module and equipment is helpful in Plant Maintenance Module.
- Exploding BOM during finished good product costing enables the SAP system to perform the costing of the components.